CHT 002 - 2D Taylor-Couette flow
In this example, conjugate heat transfer (CHT) in a quasi-2D Taylor-Couette flow is simulated.
Taylor-Couette flow, characterized by the rotation of concentric cylinders and the fascinating patterns that emerge within the fluid, exhibits diverse flow regimes depending on the rotation speeds and fluid properties.
While traditional Taylor-Couette studies often focus on fluid mechanics, incorporating heat transfer adds another layer of complexity and practical relevance. In many real-world scenarios, the rotating cylinders and the fluid have different temperatures, leading to heat exchange between them. This is where CHT simulation becomes essential.
Model definition
The model is composed of a thin disc with two hollow concentric cylinders: the inner hollow cylinder forms a solid region and the outer hollow cylinder forms the fluid region.
Demo project: Conjugate heat transfer
The model setup is based on a paper by De Marinis et al. 1
- The outer surface (at radius ) of the outer cylinder is rotating with a tangential velocity .
- The temperature at the outer surface is fixed at .
- The inner cylinder is stationary.
- The temperature at the inner surface of the inner cylinder is fixed at .
- At the interface of the solid and fluid region (surface at ), a no-slip velocity constraint is applied.
For Taylor-Couette flow, typically a viscous fluid is considered. Typical water properties are used for the fluid here, but kinematic viscosity is increased to to make it viscous. Normally, water has a kinematic viscosity of .
For the simulation setup in Allsolve, the tangential velocity is split into its X and Y components as detailed below. The heat transfer at fluid-solid interface is strongly coupled, therefore, no additional flux boundary conditions are required at the interface.
Simulation setup guide
Here you’ll find a simplified, example case level guide for setting up a conjugate heat transfer simulation in a quasi-2D Taylor-Couette flowing cylinder in Quanscient Allsolve.
Step 1 - Define variables
Start out in the Common
sidebar by defining the following variables:
Name | Description | Expression |
---|---|---|
Ro | outer radius [m] | 1.8 |
Rm | interface radius [m] | 0.9 |
Ri | inner radius [m] | 0.45 |
h | height [m] | 0.05 |
To | temperature at Ro [K] | 700 |
Ti | temperature at Ri [K] | 500 |
Uo | tangential velocity at Ro [m/s] | 2.0 |
w | angular velocity at Ro [rad/s] | Uo/Ro |
ksbykf | heat conductivity ratio between solid and fluid | 9.0 |
nu | kinematic viscosity of fluid [m²/s] | 1.0 |
Step 2 - Build the geometry
In the Model
section, build the model geometry by creating Cylinders and by using the Fragment all and Remove operations as follows.
-
Create 3 cylinders:
Name Element type Center point [m] Size [m] Rotation [deg] inner cylinder Cylinder X: 0
Radius: Ri
X: 90
Y: 0
Height: h
Y: 0
Z: 0
Z: 0
Name Element type Center point [m] Size [m] Rotation [deg] interface cylinder Cylinder X: 0
Radius: Rm
X: 90
Y: 0
Height: h
Y: 0
Z: 0
Z: 0
Name Element type Center point [m] Size [m] Rotation [deg] outer cylinder Cylinder X: 0
Radius: Ro
X: 90
Y: 0
Height: h
Y: 0
Z: 0
Z: 0
-
Apply the
fragment all
operation. -
Apply the
remove
operation, with the innermost small cylinder (volume1
) as target.
Finished geometry:
Step 3 - Define the materials
Go to the Physics
section to define the model materials.
Material 1 - Water
Assign Water
to the outer cylinder (volume 3
).
Add the target as a shared region.
- Set the Dynamic viscosity of water to
par.rho()*nu
.
Material 2 - Aluminium
Assign Aluminium
to the interface cylinder (volume 2
).
Add the target as a shared region.
- Set the Thermal conductivity of aluminium to
ksbykf*0.55
.- Here,
0.55
is the thermal conductivity of water.
- Here,
Your model materials are now defined.
Step 4 - Define the physics
Go to the Physics
section.
In this example, the Laminar flow
, Heat solid
and Heat fluid
physics are required.
Add all of them before moving on to set up interactions.
Physics 1 - Laminar flow
-
As laminar flow target, select the water region.
-
Add
Velocity constraint
.- As Target, select the water cylinder’s outer edge surface (
7
). - Set Constraint value to
[1, w * y; 1, -w * x; 1, 0.0]
. - This constraint essentially applies the constant tangential velocity
Uo
at the outer surface of the water cylinder (see model definition).
- As Target, select the water cylinder’s outer edge surface (
-
Add
Velocity constraint 2
.- As Target, select the interface surface between the fluid and solid regions (
4
). - Set Constraint value to
[1, 0; 1, 0; 1, 0]
. - This is essentially a no-slip constraint at the fluid and solid interface.
- As Target, select the interface surface between the fluid and solid regions (
-
Add
Velocity constraint 3
.- As Target, select the water cylinder top and bottom surfaces (
8, 9
). - Set Constraint value to
[0, 0; 0, 0; 1, 0]
.
- This constraint stops flow in the Z-direction through the water cylinder top and bottom surfaces.
- This is what makes the simulation quasi-2D as the velocity in the Z-direction is set to zero.
- As Target, select the water cylinder top and bottom surfaces (
-
Add
Pressure constraint
.- As Target, select points
3, 4
. - Set Constraint value to
0.0
.
- As Target, select points
-
Add the Laminar flow - Heat fluid coupling
Thermal fluid
.
Physics 2 - Heat solid
- As Heat solid target, select the aluminium region.
- Add
Constraint
.- As Target, select the aluminium cylinder inner surface (
1
). - Set Temperature constraint to
Ti
.
- As Target, select the aluminium cylinder inner surface (
Physics 3 - Heat fluid
- As Heat fluid target, select the water region.
- Add
Constraint
.- As Target, select the water cylinder outer surface (
7
). - Set Temperature constraint to
To
.
- As Target, select the water cylinder outer surface (
Your physics and their interactions are now defined.
Before moving on, check that your physics tree matches the one below.
Step 5 - Generate the mesh
Proceed to the Simulations
section to create a new mesh.
For thin geometries like in here, it makes sense to use mesh extrusion:
- Set Mesh quality to
Expert settings
. - Set Used mesher to
Basic
. - Set Scale factor to
0.15
. - Add Mesh extrusion.
- As Target, select both cylindrical volumes in the model (
2, 3
). - This creates just one extrusion layer.
Set Sublayer count in that layer to
1
. - Apply the settings and mesh.
- Check out the preview.
Finished mesh:
Step 6 - Simulate
In this step, we’ll look at:
- Setting up the steady state simulation
- How to calculate the analytical solution in your steady state simulation through scripting (optional)
- Setting up an additional sweep simulation (optional)
Steady state
Create a new simulation:
- In simulation settings:
- Set Analysis type to
Steady state
. - Set Solver mode to
Iterative solver
.
- Set Analysis type to
- In Mesh, select the mesh you created.
- In Outputs:
- Add pressure field output
p
.- As Target, select the water region.
- Add velocity field output
V
.- As Target, select the water region.
- Add temperature field output
T
.
- Add pressure field output
Your steady state simulation is now ready to run.
Scripting the analytical solution
To calculate the analytical solution, add this snippet of code to the end of your steady state simulation.py
script file:
################################################## VERIFICATION WITH ANALYTICAL SOLUTIONRo = expr.RoRm = expr.RmRi = expr.RiTo = expr.ToTi = expr.TiUo = expr.Uoksbykf = expr.ksbykf
# Analytical solution for velocitydef V(r): """https://www.researchgate.net/publication/303316864_Improving_a_conjugate-heat-transfer_immersed-boundary_method""" """https://www.princeton.edu/~gasdyn/Research/T-C_Research_Folder/Analytical_Solution.html""" if (r>Ro or r<Rm): return 0.0 else: vel = Uo * (Ro/r) * (r*r-Rm*Rm)/(Ro*Ro-Rm*Rm) return vel
# Analytical solution for temperaturedef T(r): """https://www.researchgate.net/publication/303316864_Improving_a_conjugate-heat-transfer_immersed-boundary_method""" if (r >= Ri and r <= Rm): temp = Ti + (To-Ti) * qs.log(r/Ri) / (qs.log(Rm/Ri)+qs.log(Ro/Rm)*ksbykf) return temp.evaluate() elif (r >= Rm and r <= Ro): temp = To - (To-Ti) * qs.log(Ro/r) / (qs.log(Ro/Rm)+qs.log(Rm/Ri)/ksbykf) return temp.evaluate() else: return 0.0
rT = RmTinterface_analytical = T(rT)Tinterface_simulation = (fld.T).allinterpolate(qs.selectall(), [0, rT, 0])[0]
rV = (Ro + Rm)/2.0V_analytical = V(rV)V_simulation = (fld.V).allinterpolate(qs.selectall(), [0, rV, 0])[0]
if(qs.getrank()==0): str_rT = f"@ r = {rT}m"; str_rV = f"@ r = {rV}m" print(f"{'VERIFICATION:'}", flush=True) print(f"{'':-^75}", flush=True) print(f"{'':12} {'Temperature [K]':<25} {'Velocity [m/s]':<25}", flush=True) print(f"{'':12} {str_rT:<25} {str_rV:<25}", flush=True) print(f"{'':-^75}", flush=True) print(f"{'Analytical':<12} {Tinterface_analytical:<25} {V_analytical:<25}", flush=True) print(f"{'Simulation':<12} {Tinterface_simulation:<25} {V_simulation:<25}", flush=True) print(f"{'':-^75}", flush=True)
print("NOTE: Mesh convergence can be achieved with refinement")#################################################
See Logs for verification results:
Sweep
Create a new simulation by copying the existing steady state simulation:
- Name the simulation copy as
Sweep
. - In Inputs:
- Add
ksbykf sweep
.- Set Override expression to
linspace(0.1, 20, 40)
.
- Set Override expression to
- Add
- In Outputs:
- Add custom value output:
- Name:
Max T interface
. - Output expression:
maxvalue(reg.interface_surface, T, 5)
.
- Name:
- Add custom value output:
- Name:
FSI flux
. - Output expression:
integrate(reg.interface_surface, transpose(normal(reg.aluminium)) * on(reg.aluminium, -par.k()*grad(T)), 5)
.
- Name:
- Add custom value output:
Your sweep simulation is now ready to run.
Step 7 - Plot & visualize
In the Simulations
section, add plots to see value output results, or visualizations to see field output results.
Some examples are given below.
-
Temperature field T:
-
Max T interface:
Results
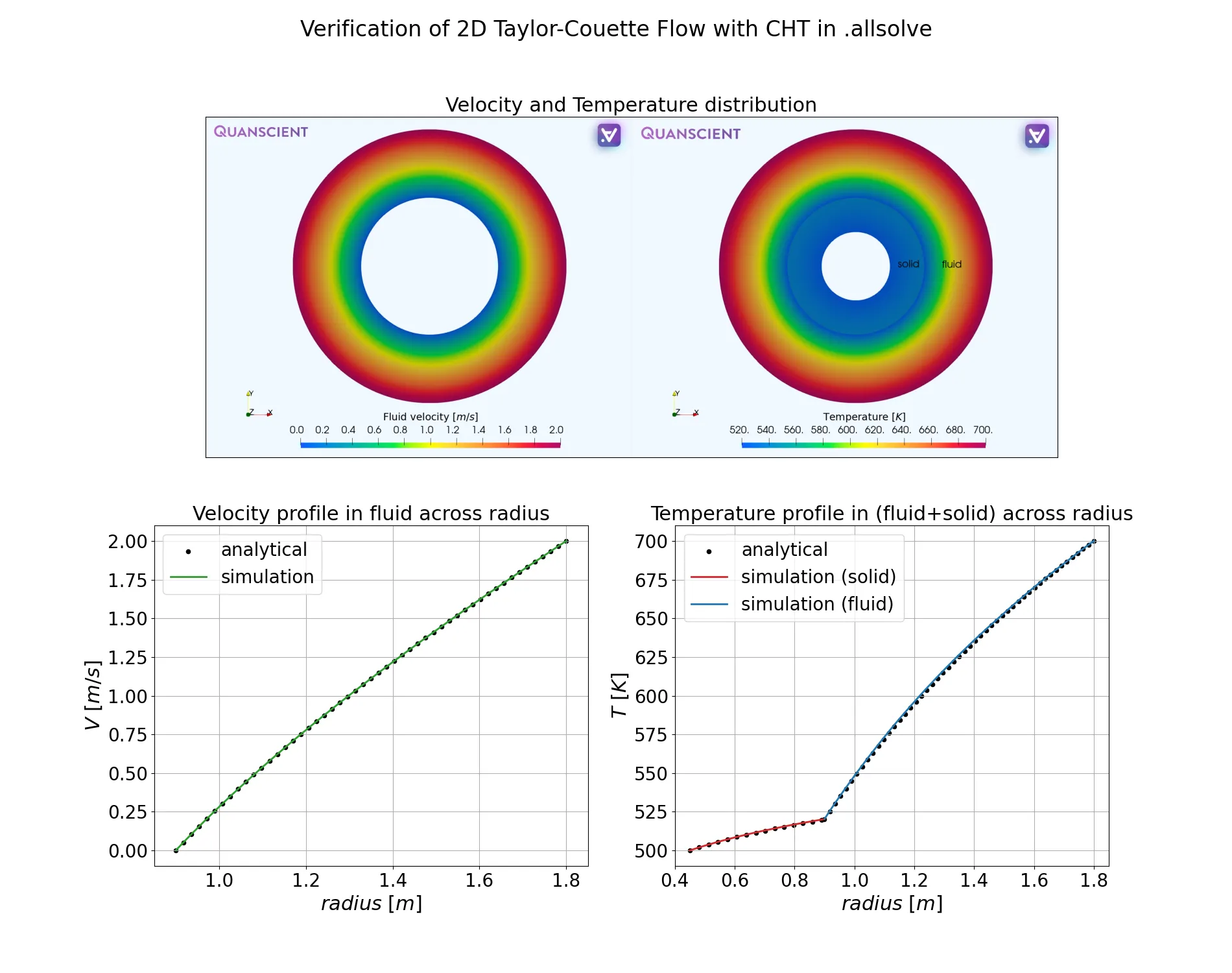
References
Footnotes
-
De Marinis, D., de Tullio, M.D., Napolitano, M. and Pascazio, G. (2016). Improving a conjugate-heat-transfer immersed-boundary method. International Journal of Numerical Methods for Heat & Fluid Flow, Vol. 26 No. 3/4, pp. 1272-1288. https://doi.org/10.1108/HFF-11-2015-0473> ↩