HB 001 - AC Joule heating
Electrical systems, from the wiring in our homes to the circuits in our smartphones, generate heat as electricity flows through their conductors. This phenomenon, known as Joule heating, can significantly impact the performance and lifespan of these systems.
Simulations are used to predict and analyze Joule heating effects. By simulating different geometries, materials, and current loads, efficiency can be optimized in wire designs. This is especially important in applications with high currents or limited space, such as electronic devices and power transmission systems.
This simulation example focuses on AC Joule heating in a 1 mm length of aluminium wire, modeled as a simple rectangular piece. By simulating the flow of alternating current, we can visualize and quantify the heat distribution and temperature rise within the conductor.
Demo project: Harmonic balance - Joule heating AC
Simulation setup guide
Here you’ll find a simplified, example case level guide for setting up a aluminium wire AC joule heating simulation in Quanscient Allsolve.
Step 1 - Build the geometry
In the Model
section, build a box for the wire geometry:
Name | Element type | Center point [m] | Size [m] | Rotation [deg] |
---|---|---|---|---|
box | Box | X: 0 | X: 1e-3 | X: 0 |
Y: 0 | Y: 1e-4 | Y: 0 | ||
Z: 0 | Z: 1e-4 | Z: 0 |
Step 2 - Define variables and materials
Go to the Common
sidebar.
-
Define a variable:
Name Description Expression freq AC frequenzy [Hz] 5
-
Assign
Aluminium
to the wire volume.- Add the aluminium target as a shared region.
Step 3 - Define the physics
Go to the Physics
section.
In this example, the Current flow and Heat solid physics are required. Add both of them before moving on to define interactions.
Physics 1 - Current flow
-
Let current flow target default to the whole geometry.
-
Add
Constraint
and name it asGround
:Name Interaction type Target Value Ground Constraint
End surface of beam in the negative X-direction ( 2
)0
-
Add
Lump I/V
:Name Interaction type Target Actuation mode Value Lump I/V Lump I/V
End surface of beam in the positive X-direction ( 1
)Current
sn(1)
Physics 2 - Heat solid
-
Let heat solid target default to the whole geometry.
-
Add
Constraint
:Name Interaction type Target Value Ground Constraint
Both end surfaces of beam ( 1, 2
)0
-
Add
Joule heating
to couple Heat solid with Current flow.- As target, select the wire volume (
1
).
- As target, select the wire volume (
Step 4 - Generate the mesh
Go to the Simulations
section.
Generate a mesh with default settings and check the preview.
Step 5 - Simulate
Create a new simulation:
Analysis type | Fundamental frequency | Harmonics |
---|---|---|
Multiharmonic | freq | 1, 2, 3, 4, 5 |
- As mesh, select the mesh you created.
- Inputs
- Add
freq sweep
with override expressionlinspace(1, 501, 41)
.
- Add
- Outputs
- Add custom value outputs:
Max T1
, output expressionmaxvalue(reg.aluminium_target, abs(harm(1, T)), 5)
Max T4
, output expressionmaxvalue(reg.aluminium_target, abs(harm(4, T)), 5)
Max T5
, output expressionmaxvalue(reg.aluminium_target, abs(harm(5, T)), 5)
- Add Electric potential field
v
and Temperature fieldT
outputs. All 5 harmonics are automatically added, but some give redundant results. Harmonicsv1, v3, v4, v5
andT2, T3
can be removed, while keeping the following harmonics:v harmonic 2
T harmonic 1
T harmonic 4
T harmonic 5
- Harmonics
v1, v3, v4, v5
as well asT2, T3
can be omitted as redundant.
- Add custom value outputs:
You simulation is now ready to run.
Step 6 - Plot & visualize results
Add plots and visualizations to see results. Some examples are given below.

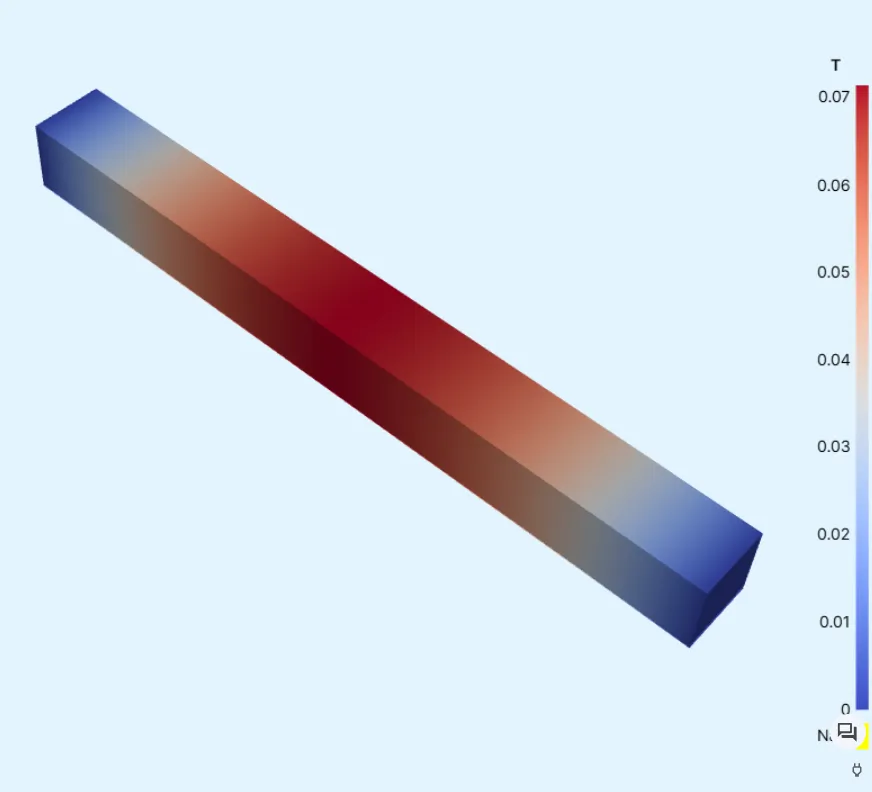